JD Hardware Wire Mesh Co., Ltd offers a specialized range of Tri-Clamp Screen Gaskets and Woven Mesh Fluid Filtration Gaskets, meticulously designed to enhance the purity and quality of various industrial processes. Our gaskets are a key component in numerous sectors, notably in pharmaceutical, food, beverage, dairy, chemical processing, water treatment, and oil and gas industries.
Our Tri-Clamp Screen Gaskets, compatible with tri-clamp fittings, are indispensable in sanitary pipe fittings. They effectively filter out particulates from fluids, ensuring the sterility and quality of the products. These gaskets are particularly crucial in industries where hygiene and purity are paramount.
In contrast, our Woven Mesh Fluid Filtration Gaskets, constructed from robust woven mesh, are engineered to separate particles from liquids and gases. These gaskets have a broad spectrum of applications, making them versatile for use in environments that demand rigorous filtration, such as in chemical processing and water treatment facilities.
Crafted from resilient materials like EPDM, PTFE, Viton, and silicone, both types of gaskets are designed to withstand harsh, corrosive, and chemical environments, thus assuring long-term functionality and efficiency. Our array of mesh sizes caters to a diverse range of filtering needs, from fine to coarse particulate removal.
The selection of our gaskets is tailored to meet the specific requirements of each application, considering factors such as the type of fluid, the nature of the particulates, and the required level of filtration, all to maintain the utmost cleanliness and purity in processing systems.
Standard Sizes of Tri-Clamp Screen Gaskets
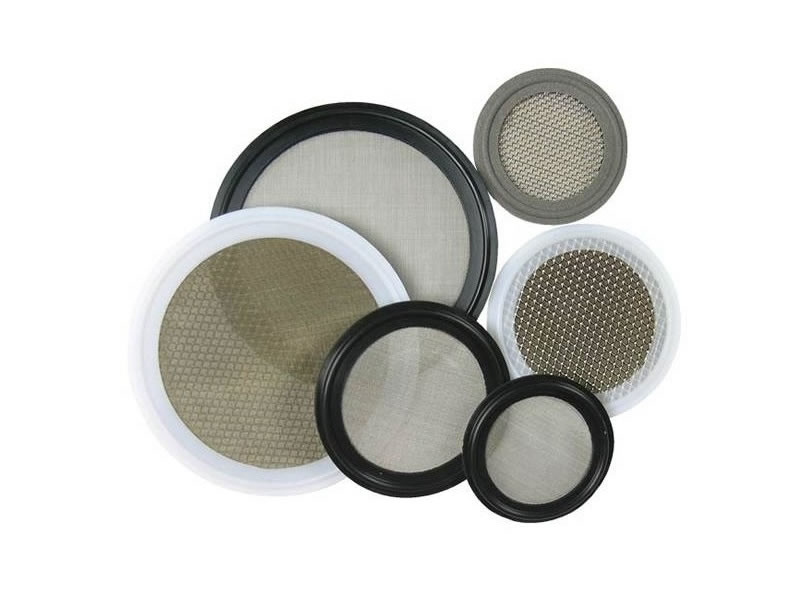
Tri-Clamp Screen Gaskets come in a variety of standard sizes to fit different tri-clamp fittings. These sizes are generally specified by the outside diameter (OD) of the gasket, which should match the OD of the tri-clamp fitting.
Common sizes include:
1/2 inch
3/4 inch
1 inch
1.5 inches
2 inches
2.5 inches
3 inches
4 inches
6 inches
8 inches
12 inches
Note: Special orders are available for metal detectable elastomers, specific screen materials, large diameters, and fine meshes. Ensure the Tri-Clamp Screen Gasket size matches the tri-clamp fitting for a secure and effective seal.
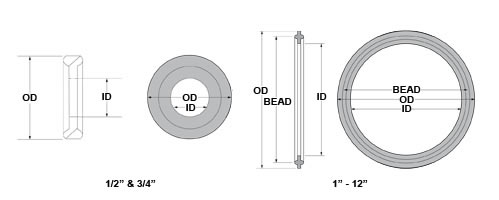
Size | Inside Diameter | Outer Diameter | Bead Diameter |
1/2″ | 0.40″ (10.2mm) | 0.87″ (22mm) | n/a |
3/4″ | 0.64″ (16.2mm) | 0.87″ (22mm) | n/a |
1″ | 0.90″ (22.9mm) | 2.00″ (50.5mm) | 1.71″ (43.5mm) |
1-1/2″ | 1.39″ (35.3mm) | 2.00″ (50.5mm) | 1.71″ (43.5mm) |
2″ | 1.88″ (47.8mm) | 2.52″ (64mm) | 2.22″ (56.5mm) |
2-1/2″ | 2.39″ (60.5mm) | 3.05″ (77.5mm) | 2.78″ (70.5mm) |
3″ | 2.88″ (73.1mm) | 3.58″ (91mm) | 3.29″ (83.5mm) |
4″ | 3.85″ (97.7mm) | 4.67″ (119mm) | 4.33″ (110mm) |
5″ | 4.86″ (123.5mm) | 5.68″ (144.2mm) | 5.29″ (134.3mm) |
6″ | 5.80″ (147.2mm) | 6.57″ (167mm) | 6.16″ (156.5mm) |
8″ | 7.80″ (198mm) | 8.56″ (217.4mm) | 8.15″ (207mm) |
10″ | 9.74″ (247.4mm) | 10.55″ (268mm) | 10.12″ (257mm) |
12″ | 11.74″ (298.2mm) | 12.56″ (319mm) | 12.17″ (309mm) |
Tri-Clamp Screen Gaskets Temperature Range
Tri-Clamp Screen Gaskets are designed to operate within a specific temperature range, which can vary depending on the material they are made from. Here are typical temperature ranges for some common materials used in these gaskets:
- EPDM (Ethylene Propylene Diene Monomer): -30°F to 300°F (-34°C to 149°C). EPDM is known for its excellent resistance to heat, ozone, and weathering.
- PTFE (Polytetrafluoroethylene): -100°F to 450°F (-73°C to 232°C). PTFE offers exceptional chemical resistance and can handle very high temperatures.
- Viton (Fluoroelastomer): -15°F to 400°F (-26°C to 204°C). Viton is highly resistant to chemicals and temperature extremes.
- Silicone: -65°F to 450°F (-54°C to 232°C). Silicone is versatile, offering good temperature resistance and flexibility.
Compare Different Materials
Tri-Clamp Screen Gaskets are made from various materials, each offering distinct advantages and suitable for different applications. When selecting a Tri-Clamp Screen Gasket, it’s crucial to consider the specific requirements of the application, including chemical compatibility, temperature range, and the nature of the substances being processed. The right material choice ensures the gasket’s effectiveness, durability, and compliance with industry standards. Here’s a comparison of their key differences and benefits:
- EPDM (Ethylene Propylene Diene Monomer)
Advantages: Excellent resistance to heat, steam, weathering, and ozone. Good flexibility and insulating properties.
Best For: Applications involving hot water, steam, and hydraulic fluids. Common in food, dairy, and beverage industries.
Limitations: Not suitable for use with oils, gasoline, and hydrocarbons. - PTFE (Polytetrafluoroethylene)
Advantages: Exceptional chemical resistance, withstands extreme temperatures, and has a low coefficient of friction.
Best For: Harsh chemical environments, pharmaceuticals, and food processing where purity and contamination avoidance are critical.
Limitations: Less flexible than other materials and can be more expensive. - Viton (Fluoroelastomer)
Advantages: Excellent resistance to oils, fuels, lubricants, and most mineral acids. High-temperature tolerance.
Best For: Environments with exposure to petroleum products, chemicals, and high temperatures.
Limitations: Not recommended for ketones, low molecular weight esters, and nitro-containing compounds. - Silicone
Advantages: High flexibility, good temperature resistance, and suitable for sterile environments.
Best For: Pharmaceutical and biotechnological applications, especially where temperature and purity are critical.
Limitations: Not ideal for applications involving oils, acids, and solvents. - Buna-N (Nitrile Rubber)
Advantages: Good resistance to oils, hydrocarbons, fats, greases, and many chemicals.
Best For: Applications with exposure to oils and fuels, like in the petroleum industry.
Limitations: Poor resistance to ozone, sunlight, and weathering; not suitable for high-temperature applications. - Mesh Material (Typically Stainless Steel)
Advantages: Durable, corrosion-resistant, and effective for filtration.
Best For: Integral to the screen gasket for particle filtration in various industrial processes.
Limitations: The choice of mesh material depends on the compatibility with the gasket material and the specific application requirements.
Woven Mesh Fluid Filtration Gaskets
These gaskets, crafted from stainless steel wires in plain or Dutch weave meshes, are ideal for high purity systems even in harsh environments. They offer a broad range of mesh sizes from 4 to 325, catering to diverse filtration needs from primary to final stages in various process equipment.
- Common Sizes of Woven Mesh Fluid Filtration Gaskets
Woven Mesh Fluid Filtration Gaskets are available in a range of standard sizes to accommodate various industry needs. The common mesh sizes range from 10 to 325 mesh, offering a spectrum of filtration capabilities. The smaller mesh sizes, such as 10 to 50 mesh, are typically used for larger particulate filtration, while sizes from 100 to 325 mesh are ideal for finer filtration requirements. This broad range ensures precise filtration in diverse applications, from primary to final process stages. - Customization Capabilities
In addition to the standard sizes, Woven Mesh Fluid Filtration Gaskets can be customized to meet specific industry requirements. Customization options extend to both the screen and gasket materials, ensuring compatibility with different fluids and operating conditions. Screen materials are available in Stainless Steel 304, 316, and 316L, known for their corrosion resistance and durability. For gasket materials, options include FKM, EPDM, Silicone, PTFE, Buna, and Tuf-Steel, each offering unique properties such as chemical resistance, temperature stability, and flexibility. The customization flexibility of these gaskets makes them suitable for a wide range of applications, including those with stringent purity and durability standards. - Size:
Mesh Size | Width of Opening(mm) | Opening | Wire Diameter(mm) | % Open Area |
Wires/Inch | Size | |||
10 x 10 | 1.905 | 0.075″ | 0.63 | 56.30% |
12 x 12 | 1.532 | 0.060″ | 0.58 | 52.40% |
14 x 14 | 1.306 | 0.051″ | 0.5 | 51.80% |
16 x 16 | 1.13 | 0.045″ | 0.45 | 50.70% |
18 x 18 | 0.979 | 0.039″ | 0.43 | 48.20% |
20 x 20 | 0.864 | 0.034″ | 0.4 | 46.20% |
24 x 24 | 0.703 | 0.028″ | 0.35 | 44.10% |
30 x 30 | 0.516 | 0.020″ | 0.35 | 37.20% |
40 x 40 | 0.381 | 0.015″ | 0.25 | 36.00% |
50 x 50 | 0.318 | 0.013″ | 0.191 | 30.30% |
60 x 60 | 0.233 | 0.009″ | 0.191 | 30.30% |
80 x 80 | 0.178 | 0.007″ | 0.14 | 31.40% |
100 x 100 | 0.14 | 0.0055″ | 0.114 | 30.30% |
120 x 120 | 0.118 | 0.0046″ | 0.094 | 30.90% |
150 x 150 | 0.104 | 0.0041″ | 0.066 | 37.20% |
180 x 180 | 0.084 | 0.0033″ | 0.058 | 34.30% |
200 x 200 | 0.074 | 0.0029″ | 0.053 | 33.60% |
250 x 250 | 0.061 | 0.0024″ | 0.041 | 36.00% |
325 x 325 | 0.043 | 0.0017″ | 0.036 | 29.70% |
Product Photo Showcase and Alias
Tri-Clamp Screen Gaskets
Ideal for corrosion-resistant environments, such as in chemical processing and marine applications.
Woven Mesh Fluid Filtration Gaskets
Suitable for screening and separating particles in the food and beverage industry.
Wire Mesh Gaskets
Appropriate for heavy-duty industrial applications like automotive and aerospace.
Process Filtration Gaskets
Used in manufacturing, particularly in the paint and coatings industry for impurity removal.
Industrial Mesh Gaskets
Geared towards large-scale applications in mining and construction for coarse material filtration.
Fluid Separation Gaskets
Utilized in water treatment facilities and oil refineries for fluid purity maintenance.