JD Hardware Wire Mesh Co., Ltd. specializes in Wire Mesh Sintering, a manufacturing process that strengthens and diversifies metal filter elements. This method layers wire mesh before undergoing sintering, transforming them into a durable, functional mesh plate.
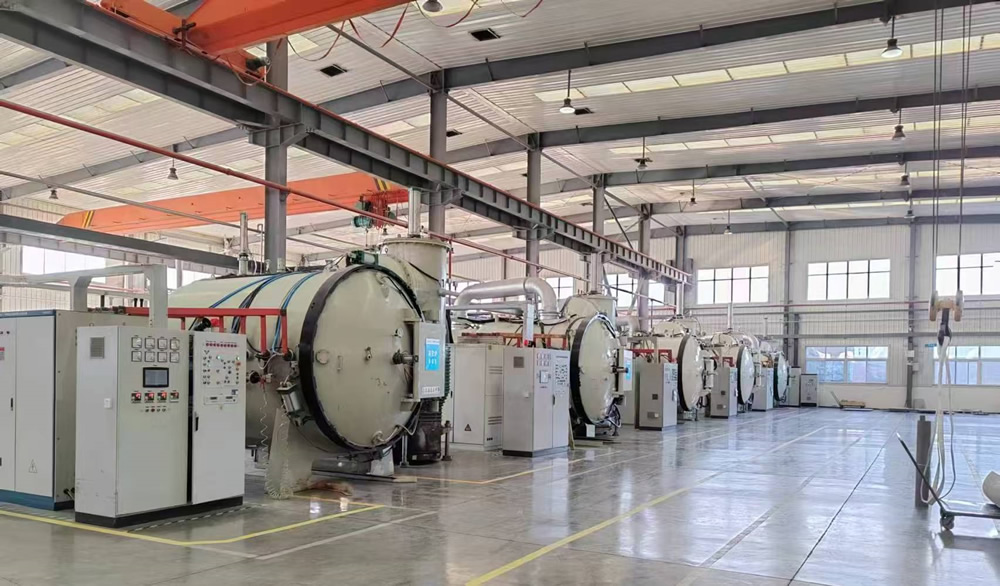
Wire Mesh Sintering Process: Known as diffusion bonding, this process fuses wires at temperatures below their melting points, creating a sturdy, porous mesh plate ideal for filtration, yet stronger than its non-sintered form.
Manufacturing Sintered Wire Mesh: Starting with defect-free wire mesh, pieces undergo pre-calendering for flatness, followed by precise lamination and spot welding to prevent shifts. In a furnace, the layers are sintered for hours, merging into a unified structure. Post-sintering, the mesh is calendered to thickness, flattened, cleaned, and dried, ready for use or packaging.
Benefits: Sintered wire mesh offers enhanced integrity, strength, and filtration capability, suitable for industrial and architectural applications. It addresses single-layer mesh issues like variable pore sizes and wire shedding by fusing wires for consistent pore size. Multi-layer sintering enhances support and protection, crucial for effective filtration. For example, sintering transforms fragile 2-micron Dutch weave wire cloth into a robust 1.7 mm thick, 5-layer mesh, maintaining its filtration rating but with increased durability.
![]() | Sintering – >> | ![]() |
Wire mesh before sintering | Wire mesh after sintering |
JD Hardware leverages advanced sintering to produce high-quality, efficient filter media, meeting the highest durability and performance standards. Our sintered wire mesh is designed for superior filtration systems and metal filter elements, providing exceptional results tailored to our clients’ diverse needs.
